Boron-aluminium
LOW-COST TECHNOLOGY OF BORON/ALUMINIUM COMPOSITES
The laboratory has developed a fabrication technology of boron/aluminium structural
elements that does not involve high-temperature/high-pressure equipment which is
usualle very expensive. This simplifies essentially the whole process of the fabrication
of tubes, shells, various profiles, etc, which is normally based on a gas isostatic
equipment.
For example, to produce boron/aluminum tubes with longitudinal reinforcement, see
Fig.1 for examples, which are characterized in Table 1, we have constructed a simple
equipment (Fig.2) based on a commercially available furnace.
Tubes have the end fittings either of aluminum or titanium alloys.
The technology provides the possibility to optimize the composite microstructure to
enhance characteristics of the tubes.
At the same time we see how to improve the technology to make the product of higher
quality and lower cost. It is certainly possible to develop similar processes for another
composite systems.
Fig.1. Boron/aluminum tubes with longitudinal reinforcement.
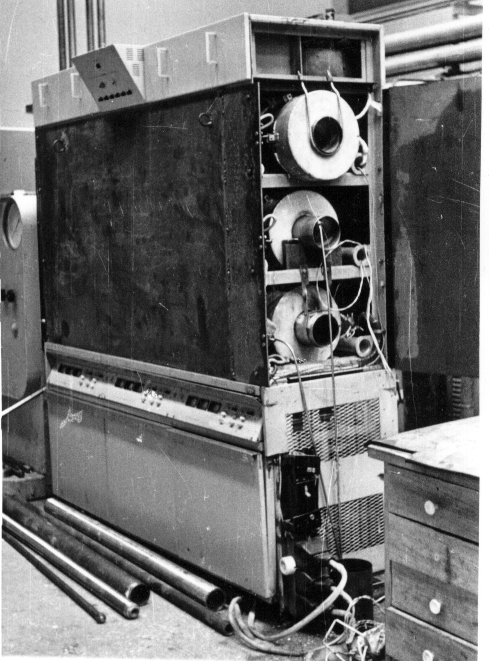
Fig.2. The equipment for producing boron/aluminum tubes with longitudinal
reinforcement. Maximum tube length is 1500 mm, maximum diameter is 75 mm.
The safety of the equipment is sufficient to run it in any room.
We propose:
- Technology transfer on the present stage of development. R&D projects in the field
of low-cost technology of metal matrix composites.
- R&D projects in the field of low-cost technology of boron/aluminium composites.
We are ready to consider the technology transfer of boron/aluminium tubes at any time.
R&D projects can be carried out in the following directions:
- Investigation of a possibility to use the technological scheme of making boron/aluminium composites in fabrication technology of SiC/Ti-composite elements.
- Improving the fabrication technology of tubes:
- Automatization of the process
- Increasing the ultimate load of long tubes under compression
- Evaluation of relationships between the test results of separate tubes in a batch and the ultimate load of a frame structure made of the tubes
- Developing the fabrication technology of shells of diameter up to 500
- Developing the fabrication technology of various open profiles.
- Developing a hybrid composite structure combining boron/carbon/aluminium composite structures.
Appendix
BORON/ALUMINIUM TUBE CHARACTERIZATION
Tubes produced by using the equipment operating at the present time:
- Maximum length: 1500 mm
- Maximum diameter: 75 mm
- Minimum diameter: 15 mm
- Maximum ratio of wall thickness to the diameter: 1:30.
Table 1. BORON/ALUMINUM TUBES.
Matrix material | Length | Diameter | Wall thickness | Tension or compression | Ultimate load |
| mm | mm | mm | | ton |
Al-6Mg | 1000 | 65 | 1.0 | Compression | 20 |
Al-6Mg | 1000 | 65 | 1.0 | Tension | 20 |
Al-6Mg | 400 | 60 | 1.2 | Compression | 40 |
Al-6Mg | 400 | 60 | 1.2 | Tension | 25 |
AD-33* | 400 | 60 | 0.75 | Tension | 18 |
* Russian trade name for the 6061-alloy.
THE EQUIPMENT IN THE LABORATORY IS CAPABLE TO PRODUCE
UP TO 1000 TUBES PER YEAR